Electrohydrodynamic jet (e-jet) printing is a high resolution printing technology where the printed liquid is driven by an electric field. Exposure to an electric field causes mobile ions in a polarizable liquid to accumulate at the liquid surface. The coulombic repulsion of the ions causes the meniscus at the nozzle end to deform into a conical shape, called a Taylor cone. When the electric field exceeds a critical limit, the stress from the surface charge repulsion at the cone apex exceeds the surface tension and a droplet of fluid is emitted towards the grounded substrate. Figure 1 shows the setup used for e-jetting. The keys to high-resolution droplet printing are to use electric field potentials below those required for atomization mode, or spray mode, as well as the use of small micropipette nozzles with diameters less than 10 μm. Deposited droplets can be as small as 240 nm with spatial accuracy in the hundreds of nm.
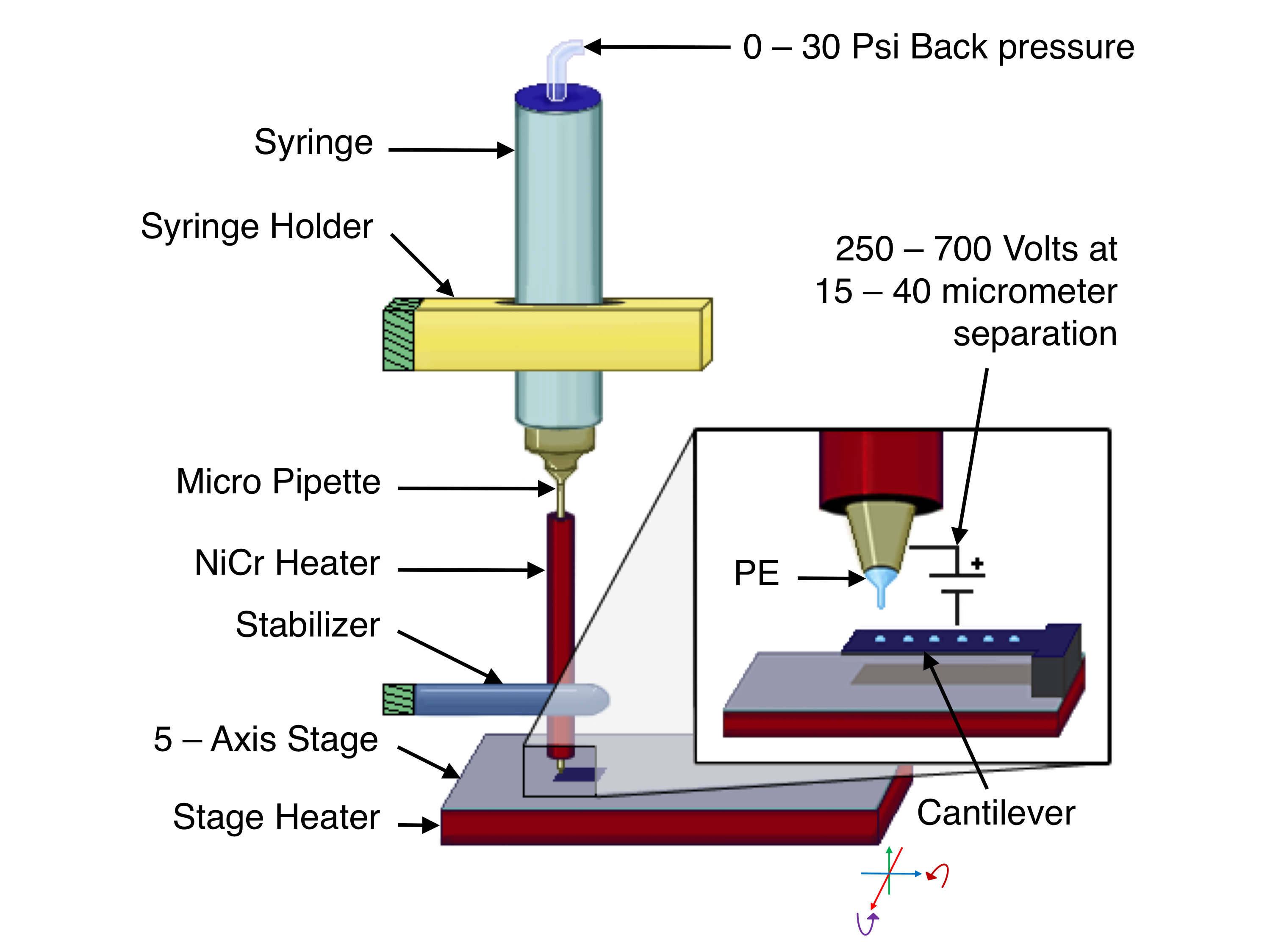
E-jet printing of polymers:
In this project, e-jet printing was used to deposit 2–27 μm diameter droplets of molten polyethylene onto microcantilever sensors. This was the first demonstration of direct e-jet printing of molten polymer. The polymer droplets were deposited as single droplets or organized patterns, with sub-μm control over droplet diameter and position. The droplet size could be controlled through a pulse-modulated source voltage, while droplet position was controlled using a positioning stage. The electrohydrodynamic method is a precise way to deposit multiple materials onto micromechanical sensors with greater resolution and repeatability than current methods.
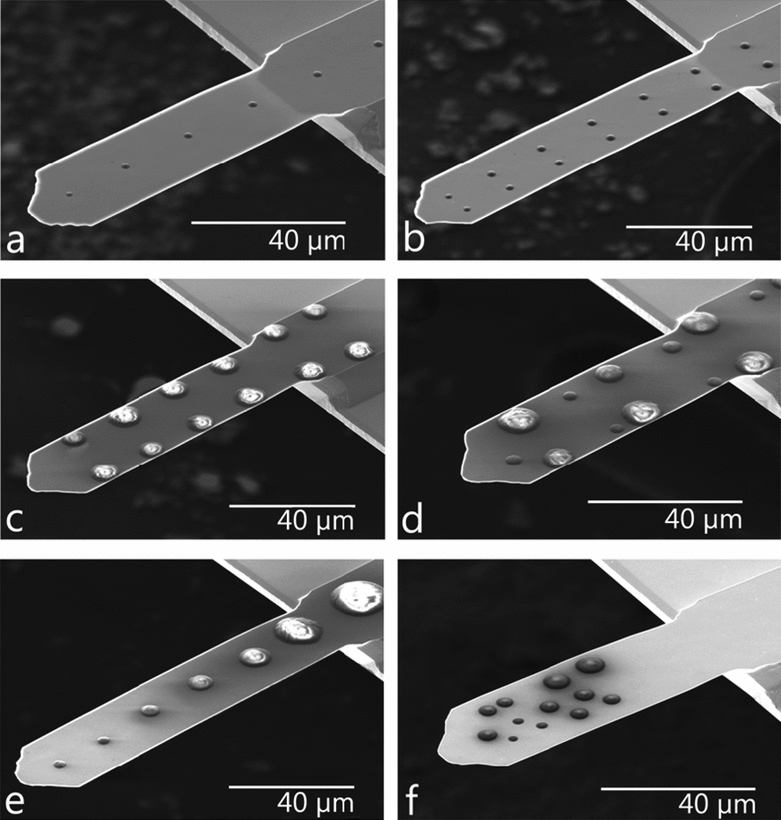
E-jet printing for integrating hydrogels into MEMS sensors:
This project used e-jet printing to integrate hydrogels onto fully suspended MEMS resonant sensor. The sensors were used to measure elastic and viscous properties of nanogram-scale samples of poly(ethylene glycol) diacrylate (PEGDA) hydrogels (MW 575 g mol−1). The hydrogel mechanical properties were then modeled and used to measure the long term mass and mechanical properties of growing cells.

Publications:
[2] Elise A. Corbin, Larry J. Millet, James H. Pikul, Curtis L. Johnson, John G. Georgiadis, William P. King & Rashid Bashir, ” Micromechanical properties of hydrogels measured with MEMS resonant sensors”, Biomedical Microdevices, vol. 15, pp. 311 – 319, 2013.
[1] James H. Pikul, Phillip Graf, Sandipan Mishra, Kira Barton, Yong-Kwan Kim, John A. Rogers, Andrew Alleyne, Placid M. Ferreira, and William P. King, “High precision electrohydrodynamic printing of polymer onto microcantilever sensors”, IEEE Sensors Journal, vol. 11, pp. 2246 – 2253, 2011.